Ion nitriding
Ion nitriding and carbonitriding:
Ion nitriding and carbonitriding in a pulsed glow discharge are the final stages in the production of any machinery construction. Increasing the solidity repeatedly, the stability and the corrosion stability. They find broad usage in the production of shafts, pivot shafts, spindles, pinions, dies for plastic ware, prints, swages, cutting instruments, etc.

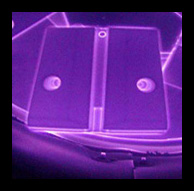
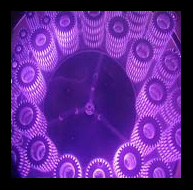
The control over the process is completely automatic. Modern controllers with colored sensorial screen for a maximum comfort during work. With the Remote Access program working under WindowsXP, Vista, Windows7 it is possible to observe and control the working process using the Internet and Ethernet web. A process history stock is provided, since a full tracking of the working regimes of the process ion nitriding aiming the best covering of the details under production. Specially developed DataViewer under Windows XP, Vista, Windows 7 is used for the graphic presentation and result printing.
A screen of for the Main regime controller – monitoring for the observation of the bicameral installation (ion nitriding) condition.
The specially developed algorithm for minimizing the temperature difference between the details guarantees for -/+ 5 degrees tapping from the processing temperature in the different areas of the working vacuum camera, combined with precise gas supplement using digital controllers of the mass volume, a homogeneousness of the formed layer, excellent structure repetition and solidity is present.
The plasmatic nitriding is done by an impulsive pulsed glow discharge formed by a dirigible plasmatic generator. Needle impulses( impulses with the highest levels of power for penetrating the plasma in long apertures ?, a better surface structure( for example: geared wheels – to avoid micro cracks, as well as impulses with a better duration used for smooth massive details. In order to keep the roughness level of the workable details (like matrixes used for extruding , etc.), and adaptive method has been invented for a precise arcing contacts with a 200nS timing.
TECHNICAL PARAMETERS
Max. weight of the processed details: ( 300 – 3500) , kg
Working volume: ( 0.2 – 5 ) , m³
Max. capacity of the plasma: (30 – 160) , kW
Capacity if the heaters: (50 – 200) , kW
Supply: 3/380V +10%/-15%, 50Hz
Gases we work with: ( nitrogen, hydrogen, ammonia, propane, argon-methane, oxygen)
tel. +359 (0)887501691 e-mail : office@termocontrol.org