Йонно азотиране
Йонно азотиране и карбонитриране:
Азотирането и карбонитрирането в тлеещ разряд са заключителени етапи при производството на дадено машиностроително изделие. Повишавайки многократно твърдоста, износоустойчивоста и корозионната устойчивост те намират приложение при производството на валове, оси, зъбни колела, шпидели, пиньони, пресформи за пластмаса, щампи, поасони, режещи инструменти и др.

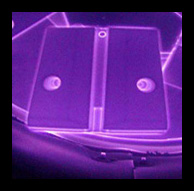
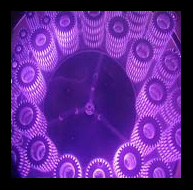
Управлението на процеса е напълно автоматизирано. Използват се съвремени контролери с цветен сензорен екран за максимално удобство при работа. Предвидена е възможност за ръчни и сервизни режими на работа. С помоща на програмата (Remote Access) работеща под WindowsXP,Vista,Vindows7 може дистанционно да се наблюдава и управлява работният процес посредством мрежата Internet, Ethernet. Предвиден е запис на процесната история, с цел пълно проследяване на работните режими на процеса йонно азотиране за най-добро покритие на обработваемите детайли. За графично представяне и отпечатване на резултатите се използва специално разработен DataViewer под WindowsXP,Vista,Vindows7.
Екран на контролера за режим Main (основен) - мониторингов за наблюдение състоянието на двукамерна инсталация за йонно азотиране.
Специално разработеният алгоритъм за минимизиране на температурната разлика на детайлите гарантира +/- 5 градуса по целзий отклонение от процесната температура в различните области на работната вакуумна камера, в съчетание с прецизното газоподаване посредством цифрови контролери на масовият обем се осигурява еднородност на формираният слой, отлична структурна повторяемост и твърдост.
Плазменото азотиране се извършва чрез импулсен тлеещ разряд формиран с помоща на управляем плазмен генератор. С управление на параметрите на импулса могат да се формират както (иглени импулси) импулси с висока пикова мощност за проникване на плазмата в дълги (глухи) отвори, подобряване на повърхностната структура (примерно: зъбни колела за избягване на микропукнатини) така и импулси с по-голяма продължителност при гладки масивни детайли. За запазване на висок клас на грапавост на обработваемите детайли (като матрици за екструдиране и др.) е разработен адаптивен метод за прецизно дъгогасене с време до 200nS.
ТЕХНИЧЕСКИ ПАРАМЕТРИ
Максимално тегло на обработваните детайли: ( 300 – 3500) , kg
Работен обем: ( 0.2 – 5 ) , m³
Максимална мощност на плазмата: (30 – 160) , kW
Мощност на нагревателите: (50 – 200) , kW
Захранване: 3/380V +10%/-15%, 50Hz
Работни газове: (азот, водород, амомяк, пропан, аргон-метан, кислород)
 тел. +359 (0)887501691 e-mail : office@termocontrol.org